Find professional packaging machine repair service for your company needs.
Find professional packaging machine repair service for your company needs.
Blog Article
Why Timely Product Packaging Equipment Repair Provider Are Important for Operational Performance
In the competitive landscape of manufacturing, the function of timely product packaging device repair services can not be overstated. Such services are vital not just for lessening unintended downtime but also for promoting a smooth manufacturing setting that fulfills customer demands. By attending to small breakdowns prior to they escalate, companies can significantly improve functional performance and reduce lasting prices. Nonetheless, the effects of disregarding these services extend beyond immediate repairs, questioning concerning equipment integrity and total productivity. What approaches can business implement to guarantee they stay positive in their maintenance method?
Impact of Downtime on Manufacturing
Downtime in manufacturing can be likened to a ship adrift at sea; without a dependable course, production processes can promptly drift off track. The effect of downtime, especially in product packaging operations, can be both instant and significant.
In addition, unplanned downtime disrupts process, leading to inefficiencies that reverberate throughout the supply chain. Workers may be left idle, causing decreased morale and efficiency. Furthermore, the price of emergency situation fixings commonly goes beyond that of arranged upkeep, further straining funds.
In a competitive landscape, where time-to-market is important, the ability to maintain regular manufacturing levels ends up being vital. Downtime not just impacts prompt result but can likewise develop a ripple impact that influences inventory degrees, capital, and overall functional effectiveness - packaging machine repair service. Hence, understanding and minimizing the impact of downtime is important for makers aiming to sustain their one-upmanship and guarantee long-term development
Benefits of Normal Maintenance
Regular upkeep of packaging machines works as an essential column in ensuring undisturbed production and operational efficiency. By carrying out a constant maintenance timetable, companies can considerably enhance the reliability and durability of their devices. Routine evaluations enable the prompt recognition of deterioration, stopping minor problems from rising right into major malfunctions.
Additionally, regular maintenance maximizes machine efficiency, guaranteeing that product packaging processes run at peak effectiveness. This optimization not only boosts throughput yet likewise reduces the chance of item problems, hence preserving top quality standards. Furthermore, well-kept makers add to power performance, minimizing functional costs connected with extreme power intake.
Along with efficiency advantages, routine maintenance cultivates a more secure working setting. By making certain that machines run properly, the threat of crashes and injuries triggered by devices failing is especially decreased. This dedication to safety and security not just shields workers however likewise lines up with regulative compliance, alleviating potential lawful liabilities.
Ultimately, spending in routine upkeep enhances general efficiency, reduces unanticipated downtime, and advertises a culture of proactive property monitoring. This calculated method makes sure that packaging procedures remain competitive in a fast-paced market, which is important for sustained success.
Expense Effects of Delayed Fixings
Disregarding timely fixings on product packaging devices can lead to significant monetary consequences for businesses. When machinery malfunctions, assembly line can halt, resulting in lost outcome and postponed delivery schedules. packaging machine repair service. Each hour of downtime translates into not only shed sales but likewise potential charges from customers as a result of unmet deadlines
In addition, postponed repair work can aggravate existing problems, causing extra severe damage and boosted repair work costs with time. A small malfunction could intensify right into a significant breakdown, requiring costly components substitute or a total overhaul of the equipment. This can stress budgets and divert funds from other vital areas, hindering overall operational development.
Furthermore, organizations may deal with enhanced labor expenses as employees remain still or are reassigned during extended repair work durations. The longer machinery runs content out solution, the extra significant the influence on workforce efficiency.
Enhancing Devices Longevity
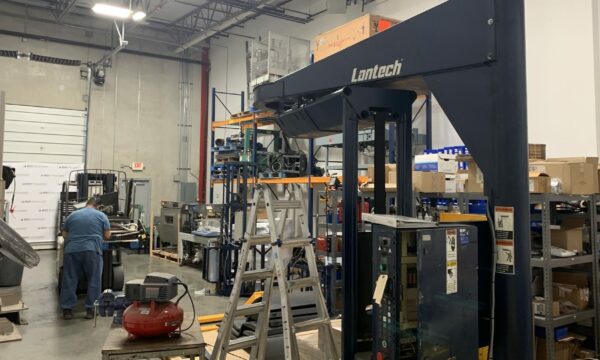
Implementing a routine upkeep schedule can determine deterioration early, avoiding little problems from rising into expensive breakdowns. This positive approach not just boosts the equipment's functional integrity however also maximizes the overall production operations. Operators ought to additionally make certain that machines are utilized according to supplier requirements to stay clear of unnecessary tension on essential components.
Furthermore, investing in high quality replacement parts during repair services adds to pop over here equipment long life (packaging machine repair service). Using low-grade parts might result in frequent break downs, negating any kind of cost financial savings realized from more affordable fixings. Proper training for drivers on best methods for maker handling and procedure can also significantly impact the equipment's lifespan
Selecting the Right Repair Service Service
Choosing the ideal fixing service for packaging devices is crucial for making sure marginal downtime and optimal performance. When reviewing possible solution suppliers, consider their market experience and field of expertise in product packaging machinery. A business with a tried and tested record in managing comparable equipment will likely have the essential experience to detect and settle concerns effectively.
Furthermore, assess the accessibility of service technicians and their feedback time to solution calls. A fixing solution that offers 24/7 assistance can dramatically reduce the effect of unforeseen machine failings. Make inquiries about their maintenance programs, as positive service can stop costly malfunctions and prolong the life expectancy of your equipment.
Examine client testimonials and reviews to evaluate the reliability and top quality of the service. A reliable fixing solution must have a history of satisfied clients who can vouch for their professionalism and reliability and effectiveness. Think about the prices included, including components and labor. While cost is necessary, focus on worth-- guaranteeing that the service fulfills your operational demands without endangering quality. By diligently selecting the ideal fixing service, businesses can improve their functional performance useful reference and minimize disruptions in manufacturing.
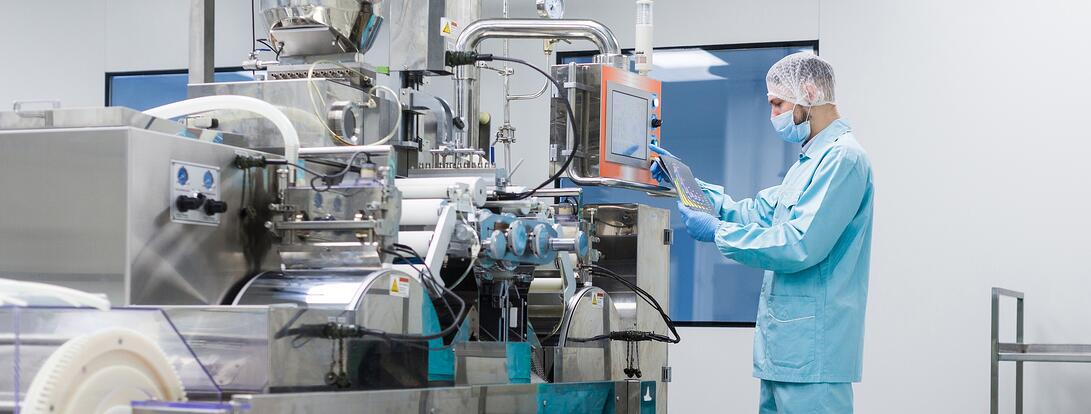
Conclusion
To conclude, timely product packaging maker fixing solutions play an essential role in maintaining operational performance. By minimizing unplanned downtime, these services not just improve production flow however additionally add to set you back savings and improved equipment longevity. Regular maintenance and punctual repair services serve to alleviate small issues before they intensify, thus guaranteeing ideal equipment performance. Ultimately, prioritizing timely repairs promotes a trustworthy supply chain, boosts worker spirits, and raises client fulfillment via regular product delivery.
Report this page